Les fabricants de composants électroniques doivent maintenir un rendement élevé tout en limitant les défauts. De légères variations de température, des propriétés des matériaux ou des réglages des équipements peuvent entraîner des défauts coûteux. Les méthodes de contrôle qualité traditionnelles détectent souvent ces problèmes trop tard—une fois les produits défectueux déjà fabriqués, expédiés, voire retournés par les clients. Pour rester compétitifs, les fabricants ont besoin d’une approche proactive capable d’identifier les variations en temps réel.
La Maîtrise Statistique des Procédés (SPC) en temps réel surveille en continu les paramètres clés de production, détectant les écarts avant qu’ils ne causent des problèmes de qualité. En analysant les données en temps réel, les équipes de production peuvent ajuster immédiatement les processus pour éviter les défauts, réduire les pertes et améliorer l’efficacité globale.
IDENTIFIER ET CORRIGER LES PROBLÈMES
Dans ce blog, nous allons nous concentrer sur le cas hypothétique d’un fabricant de matériel audio haut de gamme. Il constate une hausse des réclamations clients concernant des haut-parleurs défectueux. Les tests révèlent des irrégularités dans l’application de la colle, entraînant le décollement des cônes sous de fortes vibrations.
Si ce problème n’est pas détecté, il entraîne une augmentation des réclamations et une insatisfaction des clients. Grâce aux solutions Minitab, les équipes peuvent collecter des données directement à partir des équipements pour identifier les défauts en temps réel , dans ce cas, un PLC (Contrôleur Logique Programmable) pourrait mesurer la quantité de colle appliquée sur chaque unité. Elles peuvent envoyer ensuite les données à Real-Time SPC de Minitab pour mieux comprendre le processus, ce qui leur permet de détecter les écarts dès qu'ils se produisent. Les opérateurs peuvent ajuster immédiatement le système de distribution, évitant ainsi de futures erreurs et garantissant la fiabilité du produit.
Les alertes instantanées qu'ils reçoivent permettent aux opérateurs d'apporter des corrections immédiates.
Vous souhaitez en savoir plus sur Real-Time SPC ? Visionnez notre démonstration.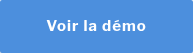
Real-Time SPC permet de résoudre les problèmes immédiats, mais le fabricant souhaite comprendre pourquoi la quantité de colle appliquée varie dès le départ.
C'est là qu'intervient le logiciel d'analyse des données Minitab.
Les ingénieurs utilisent Minitab pour analyser les données historiques des processus et identifier des tendances. Une analyse approfondie des données révèle que les incohérences dans la distribution de la colle sont liées aux fluctuations de la viscosité de la colle, elle-même influencée par la température de stockage. Le problème est plus fréquent sur les lignes de production situées près des murs extérieurs de l'usine, mettant en évidence la nécessité d'optimiser le processus.
Pour identifier la cause racine, l'équipe commence par utiliser des cartes de contrôle pour suivre le volume de colle au fil du temps, repérant des tendances qui correspondent aux variations de température. Ils utilisent une analyse de régression pour quantifier la relation entre la température de stockage et le débit de colle, confirmant que des températures plus élevées provoquent un écoulement trop rapide de la colle. Un plan d'expérience (DOE) teste ensuite diverses conditions de stockage afin de déterminer la plage de température optimale. Une fois la cause racine confirmée, l'équipe met en place un meilleur contrôle de la température et révise les protocoles de stockage, garantissant ainsi une application de colle constante et évitant les défauts à long terme.
UTILISER LES DONNÉES POUR AMÉLIORER DURABLEMENT LES PROCESSUS
En combinant Real-Time SPC avec les puissantes analyses du logiciel de statistiques Minitab, les fabricants peuvent associer des corrections réactives à une amélioration proactive de la qualité. Au-delà de la prévention immédiate des défauts, Minitab aide à révéler des tendances profondes et des problèmes systémiques qui, autrement, pourraient passer inaperçus.
Pour le fabricant de matériel audio, une analyse plus approfondie révèle que les variations saisonnières d'humidité affectent la viscosité de la colle, entraînant des variations dans la quantité distribuée. Grâce à la modélisation prédictive, l'équipe ajuste les processus en fonction des données environnementales en temps réel, garantissant une application de colle constante tout au long de l'année. Grâce à ces améliorations durables, les défauts diminuent considérablement, le rendement augmente et les réclamations clients diminuent.
LES AVANTAGES COMBINÉS DE REAL-TIME SPC ET DU LOGICIEL DE STATISTIQUES MINITAB
L'association de Real-Time SPC et de Minitab permet d'adopter une stratégie de contrôle qualité proactive et axée sur les données. Plutôt que de réagir aux défauts, les fabricants peuvent détecter immédiatement les variations et utiliser les analyses statistiques pour affiner leurs processus. Les avantages incluent :
- Détection et correction rapides des variations de procédé – Anticiper les défauts avant qu'ils ne se propagent.
- Réduction des rebuts et des coûts d'exploitation – Économiser du temps et des matériaux.
- Amélioration de la stabilité des processus – Garantir une qualité constante avec des améliorations à long terme.
- Taux de rendement plus élevés – Maximiser la production avec moins de perturbations.
- Prise de décision basée sur les données – Utiliser les données pour optimiser les processus de fabrication.
Des équipements audio aux circuits imprimés, en passant par les semi-conducteurs et les batteries, les fabricants s’appuient sur Real-Time SPC et l’analyse statistique pour garantir qualité et efficacité. Avec les bonnes solutions en place, ils détectent les problèmes en amont, évitent le gaspillage et améliorent en continu leurs opérations.
Contactez Minitab pour découvrir comment Real-Time SPC peut vous aider à optimiser votre processus.
