Every so often I get to interview someone who applies quality methodology in ways I wouldn't have imagined before I began working at Minitab. For instance, I spoke with the quality manager for a world-renowned medical center not long ago. This facility is consistently included in U.S. News and World Report's list of America’s Best Hospitals, but even the best hospitals occasionally have “sentinel events,” incidents that result in death or serious injury unrelated to the natural course of a patient’s illness.
This investigation, called a Root Cause Analysis (RCA), can be extremely complicated. The RCA is conducted by a multidisciplinary team comprising members of the affected departments. The team explores and analyzes all potential causes of the event, identifies risk reduction strategies, then implements a correction plan. “The RCA helps us carefully analyze and understand precisely what happened, and learn how how to avoid similar events in the future,” the hospital's quality manager told me. “Doing it right is critical to helping us ensure patient safety.”
The RCA team and staff involved in the event review what happened in great detail. Participants may even need to reenact the event. Meanwhile, the RCA team observes and asks questions. Were any policies or procedures breached? What role did staffing, equipment, supplies, or communication play? To find the root of the problem, it is important to keep asking “Why?” The knowledge gained from the RCA is used to develop and implement practices to reduce the risk of a similar event in the future. The plan should include a method for monitoring the effectiveness of new systems or procedures.
The RCA process can be daunting and costly. “It’s very labor-intensive, and that makes it expensive,” the quality manager explained. “We may need six to eight people on a team, and we create an enormous amount of information along the way. We want to do every RCA right, but we also want it to be as efficient and consistent as possible.”
But when the hospital began doing RCAs, existing tools made a difficult task even more challenging. “The analysis includes a host of complicated steps, and the tools we were using couldn’t handle all the things we needed to do,” the quality manager said.
That brought us to the reason for our interview: I wanted to find out how this hospital was using Minitab Engage, our process improvement software. They didn't get Minitab Engage specifically to perform Root Cause Analyses, but it turns out the software was well suited to the task.
When an RCA begins, the team uses Engage’s built-in Roadmap™ to organize the project into phases and create a launch pad for the tools used in every task. The Roadmap outlines projects and keeps them on track. As with all of Engage’s tools, the hospital was able to easily customize the Roadmap to their needs.
To develop a clear understanding of the sequence of events, the RCA team uses process maps, flowcharts, Cause-and-Effect (C&E) diagrams, and other quality forms, all of which are included in Engage’s powerful but easy-to-use built-in soft tools. And data entered into one Engage tool is available to the software’s other tools, eliminating the need to re-enter the same information. For example, information the team puts into a process map is automatically available in the C&E Matrix tool, too.
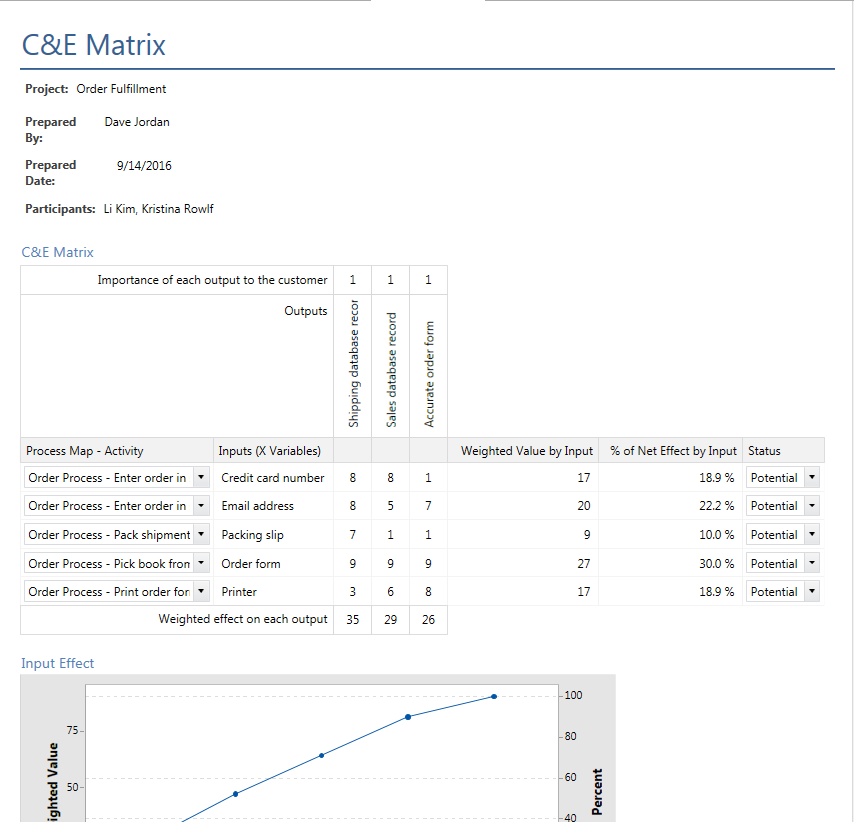
Other Engage tools that have proven useful in the RCA process include Failure Modes and Effect Analysis (FMEA), which helps identify causes for a process failure, anticipate effects, and prioritize actions to mitigate them, and the 5S audit tool, which helps determine best practices and track the implementation of improvements.
The quality manager told me it’s hard to imagine doing an RCA without Engage now. “It's just an extremely practical solution for the challenges involved,” he said. “It’s great to have all the necessary tools right at hand. We’ve also begun using Engage to map patient flow through the facility, and we anticipate we’ll be able to apply it in many other areas, too. It’s a very powerful tool for quality improvement.”
I've talked to many people about their continuous improvement initiatives, but this was certainly one of the most eye-opening interviews I've had. Regardless of the fact they use Engage, their approach to handling sentinel events vividly illustrates just how many types of issues quality improvement methods can be applied to.
What's the most unusual or unexpected application of quality improvement you've seen?