Greg Kinsey is a senior advisor in the fields of operational excellence, digital transformation, and Industry 4.0, helping industrial companies with their Industry 4.0 strategy, implementation, stakeholder buy-in and alignment, Genba engagement, and benefits realization. In January 2023, he joined the international operations consultancy and Minitab Gold Level consultant Argon & Co as a Partner, leading the Digital Manufacturing practice.
In this Blog, Greg Kinsey reveals how creative uses of the DMAIC process with digital transformation are helping factories to unlock the next level of process improvement.
Watch the reactions to Greg and the Insights Europe Conference in Zürich, Switzerland:
Read the first part of this interview: The Future of Operational Excellence according to Greg Kinsey.
Revolution of manufacturing
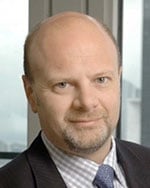
Greg Kinsey has implemented Six Sigma programs within some of the world’s top manufacturers. Hear Greg describe his relationship with Minitab during his career, and it paints a picture of the integral role of Operational Excellence in the revolution of manufacturing.
“I first met Minitab in 1994; I was the Director of Operational Excellence at Allied Signal and we deployed one of the first full-blown Lean Six Sigma programs globally. I continued to work with Minitab when I moved on to Siemens and we deployed Lean Six Sigma at Siemens. I think as I look at industry now, Minitab has become an integral part of the whole Six Sigma revolution that's happened. Most companies that I visit today, when I come into a conference room, the black belts will open their laptops and start to talk about their projects. More often than not, I see that Minitab is being used. It's an important tool for solving problems, it's an important tool for collecting and analysing the data, and it's central to the whole DMAIC process that is used in Six Sigma” explains Greg.
Digital transformation with the DMAIC Process
The digital transformation of manufacturing is broadening the toolkit and opportunities for Six Sigma’s DMAIC process, says Greg. Peel back the ‘buzz’ around Industry 4.0 and the core principles remain the same.
“Whether your problem is quality, or downtime, or bottlenecks, or whatever that might be, you need to start with a very clear definition of that problem. Then analyse the potential root causes of that problem. This is where the Black Belts come in, because typically they understand the causation, they understand many of the known or suspected root causes of problems. But also, they have the ability to explore and discover new factors or new variables that could influence that problem.”
Creativity finds 100s of new data points
For Greg, now is the opportunity for Black Belts to extend their creative thinking and domain knowledge into capturing new data through digital transformation.
“The Black Belt teams are quite creative. They will know variables that caused that a problem, it may have been one of their Black Belt focuses for years now. But say that when the sound of a machine changes, that's telling you something. Or, when the cameras see something happening, that's telling you something.
If you unlock that creativity and expand on it further, often they’ll now get to 100 or 500 variables. The idea is getting the right data, which today's technology can start to generate and build a data lake, a real-time data lake. Which then you can feed into analytical tools like Minitab and others.”
New data sources, familiar challenges
What is clear is that the fundamental principles – and challenges – remain the same, whatever your data is.
“In the data lake, getting that data cleansed, getting that data properly labelled, it's quite a lot of work involved. But again, to go back it starts with a hypothesis, ‘What data do you think you might need to better manage those processes?’ And then you build from there,” advises Greg.
“The interesting thing in today's manufacturing, the data is very siloed. If you look at a very long production line, there are pockets of data that are used locally by groups of people in their work function. And there's not a lot of sharing horizontally.”
Tackle THIS early
Greg stresses that this fragmentation is where the big wins get are often hidden, so he recommends you focus here first.
“That's usually one of the first things we tackle quite early on. We take a single production line, we look at that end-to-end final assembly, and we collect all the data. We're understanding all the pockets of data that exist in that end-to-end line. As we start to collect that up and merge that together, that gives you a basis to start to join up your processes and start to eliminate these silos.”
“Moving from a siloed organisation to a horizontally integrated organisation is one of the biggest benefits of this transformation,” says Greg.
‘Perfect time’ for the Minitab Insights Conferences
Most companies are yet to seize these opportunities in the overlap between digital transformation and Operational Excellence. Greg, with 24 years of problem-solving, training and coaching experience, is excited to speak at the Minitab Insights Europe conferences this year.
“The timing is perfect,” says Greg, who is the keynote speaker at this year’s sell-out events in Zurich and Dublin.
Minitab's Integrated Suite of Machine Learning Software can nicely complement these teams' toolkit for Predictive Analytics. Contact us to assess how Minitab can assist you in taking your Operations to the next step towards digital transformation and check our Webinar OnDemand The New Toolkit for Continuous Improvement showing an application of Machine Learning for Predictive Analytics thanks to Classification and Regression Trees (CART).
Video: Watch Greg outline the argument
Watch Greg outline his argument for why Lean Six Sigma professionals in the Minitab community should lead digital transformation:
Read the first part of this interview: The Future of Operational Excellence according to Greg Kinsey.