In manufacturing and quality control, ensuring that products meet specifications is essential. If products are “out of spec,” waste is created which ends up as scrap or rework. That’s exactly why Minitab acquired Prolink—to help manufacturers around the world automatically measure and track parts in and out of specification.
Is knowing your product is “in spec” enough? Read the blog to find out!
Need to Automate Part Measurement? Get a Demo of Prolink.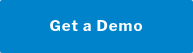
Let’s Define What Meeting Specifications Means: It’s the Minimum Standard.
When a product is "in specification," it means that its measured characteristics (such as dimensions, weight, or performance) fall within the required limits set by design or regulatory standards. In practice, this means that customers receive products that meet legal and functional requirements.
Naturally, this is critical for the current products you are measuring. But what about the ones being manufactured on the line today? Does a good batch after final inspection mean that your manufacturing process is delivering “in-spec”?
The answer is a resounding no. That’s where capability analysis comes into play.
Process Capability: Can the Process Today Produce Products That Meet Specification?
Capability analysis can be used to determine whether a process is capable of producing output that meets customer requirements, when the process is in statistical control. There are different types of capability assessments that look at different measures of process capability (just one of the many reasons Minitab’s Capability Sixpack is so popular). Most importantly, capability analysis indicates if your process – today – will most likely produce products that meet specifications.
What about tomorrow? Or in the future? Does capability cover me? Once again, the answer is no. That’s why you also need know whether or not your process is stable.
Want to Try Our Version of a Sixpack? Download a Trial of Minitab Today.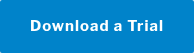
Process Stability: Can the Process Today Consistently and Predictably Produce Products That Meet Specification Over Time?
A stable process is one where variation is consistent and predictable over time, without unexpected jumps, shifts, or trends (e.g., special causes). Stability is determined using Statistical Process Control (SPC) charts, which identify when a process is in control or when corrective action is needed. Why does this matter? Because a stable process ensures long-term consistency and helps prevent defects before they happen.
To Maximize Quality, Proactively Understand If Your Process is Capable and Stable
Obviously, parts should be measured before being shipped to validate that they meet specifications. Applying statistical analysis to understand whether the process is capable and stable is equally critical to ensuring quality control. It has the added benefit of helping prevent defects from being produced in the first place, resulting in potentially material cost savings. With today’s technology, capability and stability analyses can be done in real-time, further significantly mitigating risk of defects. By employing this arsenal of techniques to your manufacturing operation, you’ll not only deliver better quality products but reduce costs and increase profits as well.
Already an Expert and Still Want to Improve? Watch Our Webinar to Learn How to Up Your Game with Real-Time SPC.