In the world of Wall Street or Silicon Valley, “high-quality revenue” is thrown around more than vests and Allbirds. It can mean different specific things for different folks, but almost all can agree that “high-quality” revenue is predictable, profitable, and diversified. What is not often talked about enough is quality as a revenue driver. Heck, Google it. Aside from getting this blog (hopefully!) or advertisements from quality management systems, you’re likely to get a lesson on “high-quality revenue.”
High-quality revenue is so important that it is usually – rightly so – at the top of the priority list for company investment. And while cost-cutting is often a priority too, rarely, if ever, do you hear organizations “investing” to save costs, unless the payoff is immediate.
Quality practitioners get a lot of credit – deservingly so – for cost savings and containment. In fact, we’re so used to associating quality with costs that we even define the very resources that prevent poor quality as cost of quality. To build on your quality initiatives you need to invest in both people and technology. Isn’t it time we reframed the conversation around quality as a revenue driver, not only to boost the necessary investment in one of the most critical areas of an organization but also to raise the profile of highest returning parts of an organization? Let’s talk about how.
Quality Accelerates Time to Market, Which Drives Revenue
Almost everyone will agree that bringing a product to the market faster is a good thing. It not only drives revenue and market share faster, but also keeps an organization ahead of or at pace with the competition.
So how does quality accelerate time to market?
1. Design Products Faster and More Reliably with Design of Experiments (DOEs). Regardless if you’re in R&D, the reliability or quality engineering departments, DOEs provide a systematic and efficient approach to exploring design space and optimizing product parameters. This allows you to significantly shorten the product design cycle and help bring products to market faster while ensuring high quality and performance. Even if you think running a DOE is difficult or too costly, predictive analytics can be a perfect partner to help you run your DOE.
See How Minitab's Design of Experiments is Used for EV Generative Braking
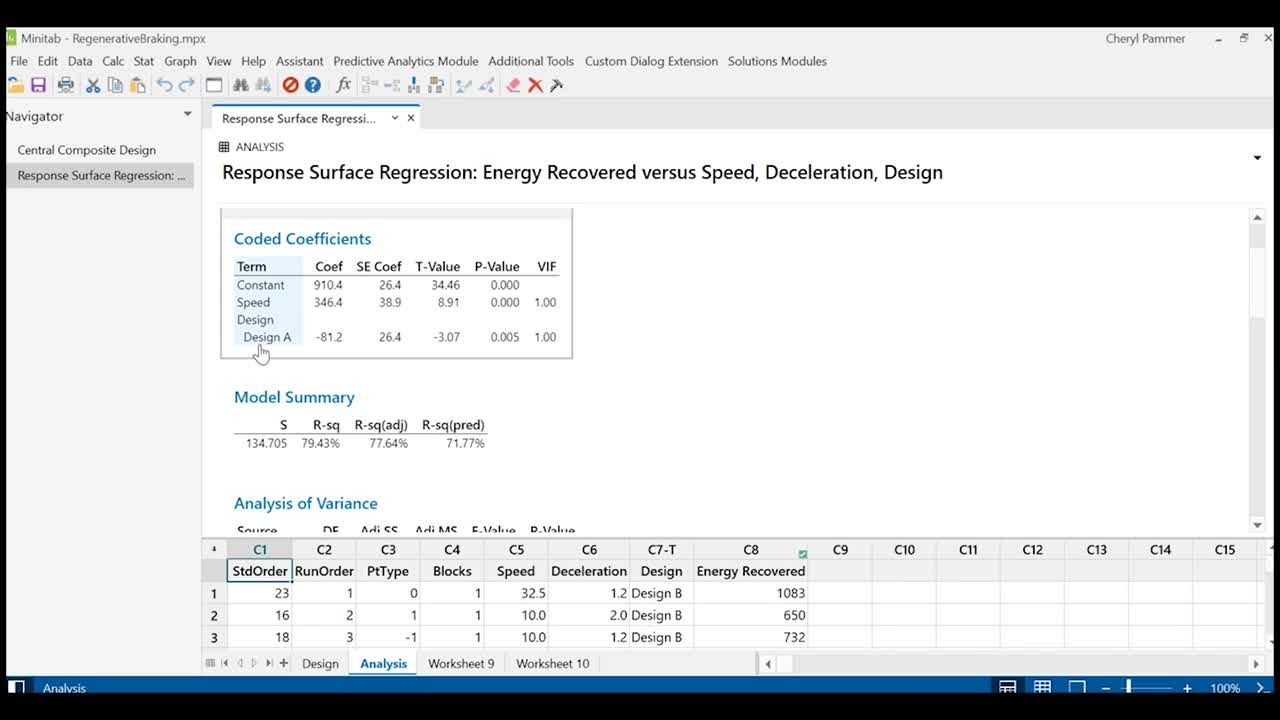
2. Use Design for Manufacturability (DFM) Approach to Minimize Manufacturing Obstacles. DFM is a proactive approach that focuses on designing products with ease of manufacturing in mind. By considering manufacturing constraints and capabilities during the product design phase, DFM helps minimize production complexities, reduce costs, and shorten lead times—ultimately accelerating time to market.
3. Use Failure Mode and Effects Analysis (FMEA) to Identify Potential Failures in Getting the Product to Market. FMEAs is a systematic method for identifying and prioritizing potential failure modes in a product or process and assessing their impact on product quality, performance, and safety. By proactively addressing potential failure modes and implementing preventive measures, FMEA helps mitigate risks, improve reliability, and expedite product development cycles. While FMEAs are popular for designing products and evaluating processes, they can be a useful tool to plan an entire product launch to mitigate risks and bring a product to market faster.
4. Statistical Process Control (SPC) Can Ensure Early Detection of Quality Issues. Using SPC techniques allow for the monitoring of manufacturing processes in real-time or your desired intervals. By analyzing process data and detecting variations or deviations from the desired specifications early on, SPC enables prompt corrective actions to be taken. This helps prevent the production of defective parts or products, reducing the need for rework or scrap and avoiding delays in the manufacturing process.
See how Real-Time SPC can improve ROI by reducing waste areas like scrap, rework, and under-performing machinery.
5. Statistical Process Control Can Also Reduce Testing and Inspection Time. SPC also enables manufacturers to establish process control limits and tolerances based on statistical analysis of process data. This allows for the reduction of redundant testing and inspection activities, as process stability and capability are continuously monitored and maintained within acceptable limits. By minimizing unnecessary testing and inspection, SPC helps streamline the production process and accelerate the time-to-market for products.
Quality Deserves the Investment, So Champion Both the Top and Bottom-Line Benefits to An Organization
Even in organizations that recognize the significant benefits quality departments offer them, rarely do they see them as a critical driver of revenues, not simply cost savings. By highlighting how investments in quality can help bring products to market faster, quality teams can get the resources necessary to have an even bigger impact.
Ready to make your quality initiatives a key driver of revenue?