Electronics manufacturers must maintain high yield while keeping defects low. Even small fluctuations in temperature, material properties, or equipment settings can lead to costly defects. Traditional quality control methods often catch these issues too late—after defective products have already been produced, shipped, or even returned by customers. To stay competitive, manufacturers need a proactive approach that detects variations as they happen.
Real-Time Statistical Process Control (SPC) continuously monitors key production parameters, identifying deviations before they result in quality problems. By analyzing data in real time, production teams can make immediate adjustments to prevent defects, reduce waste, and improve overall efficiency.
Identifying and Fixing Issues
For this blog post, our use case will focus on a hypothetical manufacturer producing high-end audio equipment. They are starting to see an uptick in customer complaints about faulty speaker drivers. Testing shows inconsistencies in the glue application process, which causes the speaker cones to detach under high vibrations. Left undetected, this issue leads to increased warranty claims and customer dissatisfaction. With Minitab’s solutions, teams can collect data right out of equipment to identify defects in real-time; in this case, perhaps a PLC (programmable logic controller) is measuring the amount of adhesive poured onto each unit. Then, they can send the data to Real-Time SPC to get a better understanding of the process, enabling them to catch deviations as soon as they occur. Operators can adjust the dispensing system immediately, preventing future mistakes and ensuring product reliability.
The instant alerts they receive enable the operators to make immediate corrections.
Interested in learning more about Real-Time SPC? Watch our brief demo. 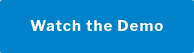
Real-Time SPC helps fix immediate issues, but the manufacturer wants to understand why the amount of adhesive poured varies in the first place.
That’s where Minitab Statistical Software comes in.
Engineers use Minitab to analyze historical process data and identify patterns. A deep dive into the data reveals that dispensing inconsistencies correlate with fluctuations in adhesive viscosity, which is affected by storage temperature. The issue is more common on production lines near exterior walls of the facility, highlighting the need for process optimization.
To pinpoint the root cause, the team starts with Control Charts to track adhesive volume over time, identifying patterns that align with temperature changes. They use Regression Analysis to quantify the relationship between storage temperature and adhesive flow, confirming that warmer conditions cause the adhesive to dispense too quickly. A Design of Experiments (DOE) study further tests different storage conditions to determine the optimal temperature range. Once the root cause is confirmed, the team installs better climate controls and revises storage protocols, ensuring consistent adhesive application and preventing defects long-term.
Using Data to Drive Long-Term Process Improvements
By combining Real-Time SPC with Minitab Statistical Software’s powerful analytics, manufacturers can combine reactive fixes with proactive quality improvement. Beyond immediate defect prevention, Minitab helps uncover deeper trends and systemic issues that might otherwise go unnoticed.
For the audio equipment manufacturer, further analysis reveals that seasonal humidity changes affect adhesive viscosity, leading to variations in the amount dispensed. Using predictive modeling, the team develops process adjustments based on real-time environmental data, ensuring consistent adhesive application year-round. With these long-term improvements, defects drop significantly, yield increases, and customer complaints decrease.
The Combined Benefits of Real-Time SPC and Minitab Statistical Software
Bringing Real-Time SPC and Minitab together enables a proactive, data-driven quality control strategy. Instead of reacting to defects, manufacturers can detect variations immediately and use statistical insights to refine processes. The benefits include:
- Faster detection and correction of process variations – Prevents defects before they spread.
- Reduced scrap and rework costs – Saves time and materials.
- Improved process stability – Long-term improvements lead to consistent quality.
- Higher yield rates – Maximizes output with fewer disruptions.
- Data-driven decision making – Uses insights to optimize manufacturing processes.
From audio equipment to circuit boards, semiconductors, and batteries, manufacturers rely on Real-Time SPC and statistical analysis to maintain high quality and efficiency. With the right tools in place, they can catch issues early, prevent waste, and continuously improve operations.
Talk to Minitab to learn more about how Real-Time SPC can benefit your organization.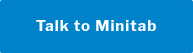