Transportation operations are the backbone of countless industries, but even small inefficiencies can compound over time, quietly draining resources and reducing profitability. By embracing a mindset of continuous improvement and leveraging powerful tools like Minitab, you can identify and address these inefficiencies systematically—turning obstacles into opportunities for growth.
Let’s explore three common inefficiencies in fleet operations and how to resolve them with data-driven improvements.
1. Excess Fuel Consumption
Fuel costs are a significant and ongoing expense for any fleet. Inefficient routes, idling vehicles, and inconsistent driving behaviors all contribute to wasted fuel. For instance, a fleet might discover that drivers are using outdated routes that increase travel time and fuel consumption.
Solution:
Start by analyzing your fuel data to pinpoint patterns and outliers. With Minitab’s Regression Analysis, you can identify the factors that contribute most to excessive fuel consumption, such as idle times, route inefficiencies, or vehicle maintenance issues. Use Pareto Charts to prioritize these factors based on their impact.
Once you know where improvements are needed, implement changes incrementally, such as optimizing routes or introducing driver training programs. Track the results over time using Control Charts to ensure sustained improvements.
2. Delays and Delivery Disruptions
Delays aren’t just frustrating; they’re costly. Whether caused by unexpected vehicle breakdowns, poorly timed maintenance, or traffic congestion, they can lead to missed deadlines and decreased customer trust. A fleet might find that its reactive approach to maintenance is leading to frequent breakdowns during critical delivery windows.
Solution:
Shift from reactive to predictive maintenance. Minitab’s Predictive Analytics can analyze historical maintenance data and identify trends, helping you anticipate when vehicles are likely to require servicing. Use Control Charts to monitor vehicle performance over time and detect early warning signs of potential issues.
With a data-driven maintenance schedule in place, you can reduce downtime, improve reliability, and ensure deliveries remain on track. Continuous monitoring ensures that your operations adapt as conditions evolve, reinforcing improvements.
Watch our demo to see how Minitab can help enhance your supply chain.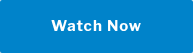
3. Underutilized Resources
Underutilization of vehicles, drivers, or storage space often goes unnoticed, but it can lead to wasted capacity and inflated costs. For example, a fleet might regularly send out partially loaded vehicles, requiring additional trips to meet demand.
Solution:
Start by consolidating your data. Minitab Connect’s Data Preparation Tools allow you to integrate information from shipment schedules, delivery volumes, and driver availability into a single view. Use Design of Experiments (DOE) to test different strategies for load planning, scheduling, and routing.
Once you’ve identified optimal resource allocation strategies, implement them gradually, tracking results with Run Charts to measure improvements. Over time, you’ll see increased utilization, fewer trips, and greater cost savings—all while maintaining flexibility for unexpected changes.
The Power of Continuous Improvement with Minitab
Every inefficiency is an opportunity to improve, and the journey to optimization is never truly complete. By embracing a culture of continuous improvement and using Minitab’s tools to uncover insights and track progress, your fleet can achieve long-term success.
Ready to take the next step toward greater efficiency and profitability?