Though I never received formal training in continuous improvement methodologies or philosophies, my mindset has always been about finding ways to get better. Before I joined Minitab, I wasn’t aware of so many formal methodologies to improve. Much like martial arts, many of the methodologies have similarities, and are comprised of philosophies as much as techniques. Here’s an effort to help introduce them to you (and this is in no way an exhaustive list). Perhaps it will encourage you to dive deeper into one that speaks to you and help you on your personal or professional journey.
Types of Strategies
Plan-Do-Check-Act (PDCA). This simple, yet effective concept is the basis for most continuous improvement efforts. By setting a goal, taking actions, measuring impact and implementing the improvement, most methodologies fall under this general method. More specifically, however, the PDCA method also refers to a methodology used to improve a process or product by breaking it down into steps and improving each step.
Kata. Originating in martial arts, "kata" are structured routines consisting of patterns. With regards to continuous improvement, Kata is a repetitive four-step routine, built on the Plan-Do-Check-Act philosophy that, when practiced, can build a habit of thinking and working creatively and scientifically to build a culture of improvement and innovation in an organization. The Kata methodology is a broader concept applicable to various fields for skill development and operational improvement.
Lean. Lean is both a mindset and a methodology. Philosophically, a lean organization encourages everyone to spot waste and bring it up to management to be addressed. The methodology that focuses on maximizing customer value while minimizing waste and eliminating defects. Lean methods use data but rely more on specific Lean tools to better understanding a process, look for waste and prevent mistakes. Learn more by discovering 10 critical Lean tools that could help you streamline your processes, eliminate waste, and boost productivity across your organization.
Want to Start Trying Out lean Tools? Download a Free Trial of Workspace.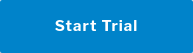
Six Sigma. Based on the concept of achieving Six Sigma quality (or improving long-term levels below 3.4 defects per million opportunities), Six Sigma is one of the most popular continuous improvement methodologies. Well known for its DMAIC process comprised of Define, Measure, Analyze, Improve and Control, Six Sigma practitioners use statistics, financial analysis, and project management to identify and reduce defects and errors, minimize variation, and increase quality and efficiency. Over time, Six Sigma has expanded from a quality focus to a more general business concept that helps organizations better meet customer requirements and improve products, processes and services.
Lean Six Sigma. Not surprisingly, Lean Six Sigma combines the best of both approaches, leveraging speed and waste reduction from Lean with the rigor (and statistical analysis) of Six Sigma in eliminating defects. Looking for a guide? Here’s a link to a best-selling book that can help you on your journey.
Kaizen. Translating from Japanese, Kaizen literally means “good change”, “change for the better”, or “improvement.” The Kaizen philosophy focuses on continuous improvement from all employees at a company and reaches across all business functions and processes. Kaizen is often designed to address a particular issue over the course of a week, which is referred to as a “kaizen blitz” or “kaizen event,” which are focused on projects that can accomplish breakthrough improvements in a short amount of time.
Toyota Production System (TPS). According to Toyota, the Toyota Production System is “an original manufacturing philosophy that aims to eliminate waste and achieve the best possible efficiency.” Similar to Kaizen, TPS is an organizational culture as much as it is a factory operating system focused on providing the best quality, lowest cost, and shortest lead time through the elimination of waste. Always on the cutting edge of quality improvement, learn how Toyota has implemented Minitab Real-Time SPC and predictive analytics to reduce the rate of non-conformity of front-end adjustments on the Yaris and Yaris Cross from 5% to 0.15% and are relying on Minitab to achieve their goal of a 0% non-conformity rate.
Toyota Kata. Unlike TPS, Toyota Kata was not actually created by Toyota. Toyota Kata is a systematic approach for developing continuous improvement habits that stick, developed by Lean expert Mike Rother's management book: Toyota Kata: Managing People for Improvement, Adaptiveness, and Superior Results. His method builds on Toyota’s process, but adapts lessons learned from the production line into an improvement strategy. Unlike the regular Kata, Toyota Kata is a specific methodology with a clear structure and purpose tailored to continuous improvement in business and manufacturing. Toyota Kata also involves specific roles (learner and coach) and a highly structured routine (Improvement and Coaching Kata).
Kanban. Another offshoot of TPS, Kanban is a visual workflow management method used for continuous improvement, often associated with lean and agile practices. It has evolved from its origins in manufacturing and is now popular in various industries, including software development and service industries. The core tool in Kanban is the Kanban board, which visually represents the workflow. It typically includes columns such as "To Do," "In Progress," and "Done."
Scrum. Made popular in the software industry, Scrum is an agile framework used for managing and completing complex projects. Scrum integrates continuous improvement through regular inspection, adaptation, and team reflections. Using this methodology, projects are broken down into sprints (typically anywhere from 1-4 weeks) during which the team works to complete the Sprint Backlog. By breaking down the project, with daily meetings, regular feedback from stakeholders and transparency, this methodology allows an organization to tackle projects and drive improvements.
Theory of Constraints (TOC). The Theory of Constraints (TOC) is a management philosophy developed to identify and manage the bottleneck or constraint (either physical or a policy or a process) that limits the performance of a system. This structured approach involves identifying the constraint, exploiting the constraint (i.e. optimizing the use of it), subordinating everything else (i.e. ensure that non-constraint resources do not produce more than the constraint can handle), elevating the constraint (i.e. taking actions to increase the capacity or capability of the constraint) and repeating the process to identify the next constraint.
Total Quality Management (TQM). Total Quality Management is a comprehensive management approach focused on improving the quality of an organization’s outputs, including goods and services, through continuous improvement of internal practices. TQM emphasizes customer satisfaction, employee involvement, and systematic problem-solving. This approach leverages many of the aforementioned methodologies like Kaizen, PDCA, Six Sigma and more.
Get in touch with Minitab today to learn more.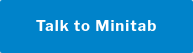