故障モード影響解析(FMEA)は、生産技術で一般的に用いられている方法で、設計、製造、組み立て工程、または製品やサービスで起こりうるすべての故障を特定します。
始まりは米軍規格でしたが、やがて自動車産業はFMEAの基準を定めていきました。そして他の産業界も、自動車産業におけるリスク解析の最善な実例を取り入れ、継続的に実践しています。
FMEAとそのメリットの詳細に興味をお持ちですか?
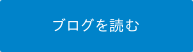
自動車産業の品質基準ガイドラインは、全米自動車産業協会(AIAG)およびドイツ自動車工業会(VDA)の主要2団体が提供しています。
経済のグローバル化が進み、メーカーは世界中のあらゆる場所から簡単に自動車用品や構成部品を調達できるようになりました。しかしながら、FMEA手法が2種類あることは、非効率的で自動車産業の進歩を妨げます。たとえば、北米とドイツのどちらの取引先にも部品供給を行っている業者は、同じ部品でも向け先によって評価方法を変えなくてはいけませんでした。また、メーカーの方も、業者の監査を行う際、地理的な位置で得る評価システムが変わっていました。これにより、供給業者の慣行を比較すること、さらにはリスクを評価することが、困難で時間のかかるものになっていました。
全体的に見ると、2種類の基準があることで、混乱が生じ、世界中の供給業者やメーカーの製品開発や工程改善の複雑さが増していました。
AIAG-VDA FMEAの主な変化
全米自動車産業協会(AIAG)とドイツ自動車工業会(VDA)は協力して、防止に重きを置いてリスク軽減を優先するFMEA手順の標準版を作成し、2019年、自動車産業に一貫した方向性とガイダンスを提供しました。自動車産業全体でメーカーの要件を満たせるように設計された単一評価表は、混乱のリスクを低減させ、作業の重複を減少させるものです。この国際的な共通のガイドラインがあれば、自動車産業は世界中のすべての顧客のニーズと期待に応えながら、単一のFMEA手順を管理できます。
以前の地域マニュアルでは、問題の重大度、発生頻度、検出可能性がすべて等しく重み付けされていましたが、これとは対照的に、新しい評価フレームワークには階層があります。今後は、問題の重大度、発生頻度、検出可能性の順に最重要視されます。つまり、新しい手法では、重大な問題への対処が優先されます。たとえその発生頻度が少なくて検出が容易であったとしても、重大性が高ければ、発生頻度の多い問題や検出の難しい問題よりも優先されるのです。
AIAGとVDAの協力から生まれた改定FMEAの新しい7つの手順は、3つのカテゴリに分類できます。
ステップ1~3はシステム解析です。
- 計画と準備
- 構造分析
- 機能分析
ステップ4~6は故障解析とリスク軽減です。
- 故障分析
- リスク分析
- 最適化
ステップ7は結果を文書化して、リスクを周知させるものです。
以下は、Minitab Workspace®および最新のAIAG-VDA FMEAフレームワークをサポートするために作成されたMinitab EngageTMにある設計故障モード影響解析(DFMEA)テンプレートフォームの事前レビューです。工程故障モード影響解析(PMFEA)テンプレートも、両方の製品で使用可能です。DFMEAを使うのとPMFEAを使うのでは手法的な違いがあることは明らかですが、どちらにもAIAG-VDA FMEAの7手順が組み込まれています。
Minitab の AIAG-VDA FMEAテンプレートの役立て方
FMEAを使用する自動車産業の業者は、最新AIAG-VDA FMEA手法を実施する時、評価フレームワークの変更と、アプローチおよび用語の変更の両方に注意を払いながら、入念かつ綿密に行う必要があります。
FMEAを徹底的に確認するには時間、理解、労力が必要ですが、Minitab Workspace®およびMinitab EngageTMの専門的に設計されたDFMEAおよびPFMEAのフォームテンプレートを活用することで、自社のFMEAが最新の自動車産業基準に沿っていることに自信を持ちながらリスク分析手順を更新できます。
Minitab WorkspaceでAIAG-VDA FMEAテンプレートをお試しになりますか?
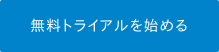