The importance of reducing defects spans industries—whether you work in automotive manufacturing, electronics production, pharmaceuticals, or operate within a large manufacturing space. Defects in production can be costly, leading to rework, delays, and inefficiencies that directly impact the bottom line.
An example of this can be seen in the semiconductor manufacturing industry. Statistical analysis in manufacturing has become increasingly critical. Typically, semiconductors are sold directly to large companies, distributors, or resellers. If defects occur in the manufacturing process, they can ripple through the supply chain, resulting in significant financial losses and operational challenges.
Methods to Reduce Defects in Semiconductors
We generated a hypothetical data set that mirrors what is often seen in the industry. In this example, the semiconductor manufacturer was experiencing a long stretch of days with higher-than-average defect rates in tested semiconductors.
In this scenario, the team calculated higher-than-average defect rates in 41 out of the past 50 days. They included the data they collected from these days, such as solder temperature, line speed, and humidity percentage. The team surmised that any of these factors—or a combination of them—could have contributed to these defects.
Then, we used Minitab Statistical Software and applied Stepwise Binary Logistic Regression to determine whether any of these factors had a statistically significant impact on the defect rates. Here's what Minitab produced:
The results reveal that humidity is a significant predictor of defect rates in semiconductors with a P-Value of .017. This demonstrates a clear impact on product quality. For every 1% rise in humidity, the likelihood of a defect increases by 13.1%. In practical terms, maintaining controlled humidity levels in the production environment could substantially reduce defects, ultimately improving yield rates and customer satisfaction.
Minitab’s Binary Fitted Line Plot helps visualize this relationship. As humidity increased, so did the likelihood of defects:
Make Improvements
To tackle the humidity-related defects in semiconductor production, the team could use a Failure Modes and Effects Analysis (FMEA) in Minitab Workspace to assess potential risks.
In this example, they might identify issues like poor solder joints, increased oxidation, and weak component bonding, all of which could be exacerbated by high humidity. The team would then rank these risks based on their severity, likelihood, and detectability. The highest-priority actions could focus on more effectively controlling humidity in key areas, closely monitoring humidity levels, and improving the overall environment in the production facility. These steps would aim to reduce defects and improve product quality by ensuring that humidity stays within the optimal range.
Want to learn more about Minitab Workspace? Download our complimentary resource "3 Common Problems Workspace Can Solve"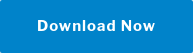
Better Product Quality, More Secure Bottom Lines
Reducing defects often starts with addressing the root causes in your manufacturing process. In the case of semiconductor manufacturing, identifying humidity as a key factor in defect rates helped the team take targeted actions. By using tools like Minitab and FMEA, they could prioritize improvements that would directly reduce defects, ensuring better product quality and more efficient operations. Ultimately, these efforts contribute to smoother production processes and a stronger, more secure bottom line.